Perma Pure
Nafion® Sample gas dryer
There are many reasons for drying sample gases for analysis, be it that the operating temperature of the analyzer is below the dew point temperature of the sample gas or that the analysis is disturbed by higher water concentrations. Conventional sample gas dryers such as condensate coolers, adsorption dryers or permeation dryers often change the composition of the sample gas by partially precipitating the sample component with the condensate, adsorbing it with the water or permeating it with the water. Drying with a Nafion® membrane, on the other hand, is based on a water-specific chemical process.
Principle of drying with Nafion® sample gas dryers
Nafion® is a copolymer of perfluoro-3,6-dioxa-4methyl-7octene sulfonic acid and tetrafluoroethylene.
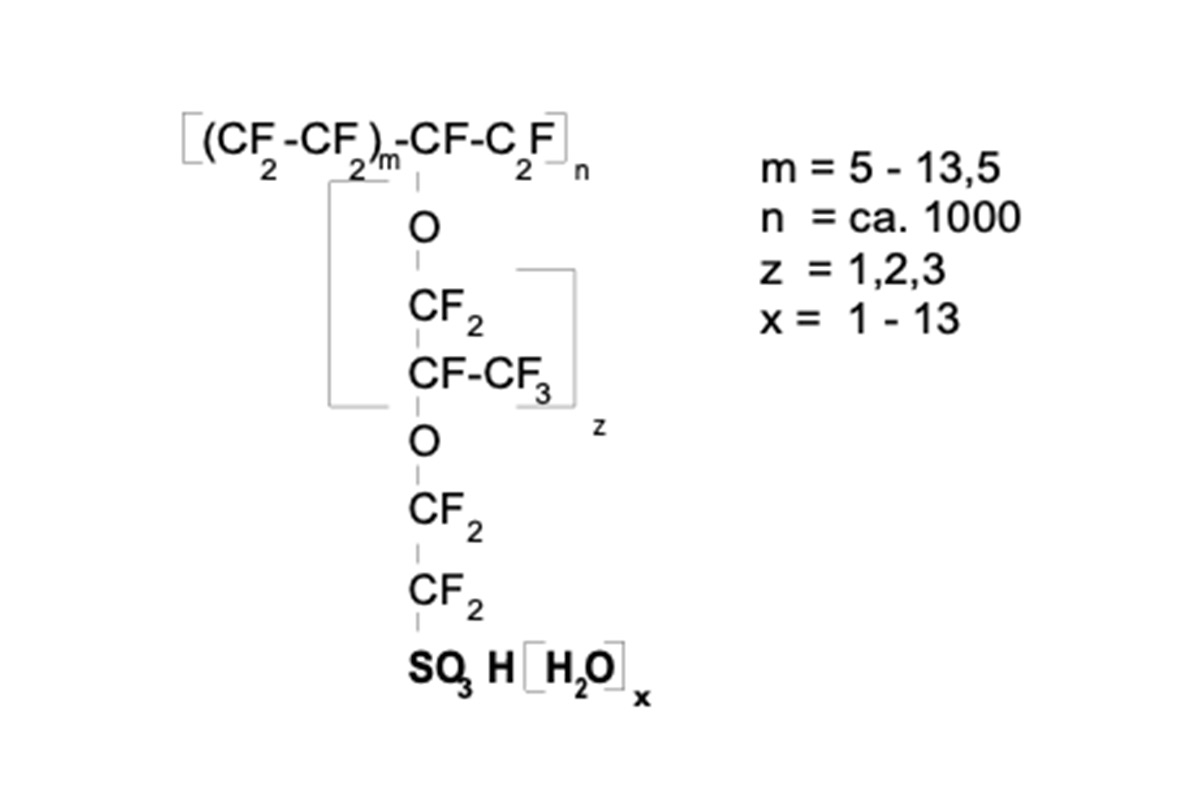
Nafion® spontaneously absorbs water while its in its gaseous phase.
Each sulphonic acid group is surrounded by a maximum of 13 water molecules. The sulfonic acid groups form ion channels within the polymer through which water molecules can be transported. When water touches a sulfonic acid group on the outside of the Nafion® film, it is momentarily bound by the group. Other sulfonic acid groups inside the wall now have a higher affinity for water because they have not yet bound any water. The water is consequently transported through the ion channels until the other side of the wall is reached and the Nafion® wall is saturated. This transport is rapid. If the water vapor partial pressure in the vicinity of the Nafion® wall is lower than in the Nafion® membrane itself, water is released into the atmosphere in the form of vapor – until the difference in water vapor partial pressure between the atmospheres on both sides of the wall is equalized. Water is always transported in the direction of the lower water vapor partial pressure. For the continuous drying of gases, the Nafion® is extruded as a pipe. A Nafion® tube or a bundle of Nafion® tubes is surrounded by a housing and can thus be supplied with a drying gas in counterflow. This continuously maintains a water vapor – partial pressure gradient.
Temperature and pressure influences, material properties
Nafion® is stable up to a temperature of 160° C, but the housing material and the head of a tube bundle set lower limits. A gas temperature of 150° C must not be exceeded even when using PTFE or stainless steel housings. The amount of residual water in the Nafion® wall is very temperature-dependent. At higher temperatures, the water is retained more by the wall than at lower temperatures and therefore cannot be released into the dry gas. The water concentration inside the Nafion® wall corresponds to the water concentration in the atmosphere outside the Nafion®. If the water concentration value in the moist sample gas reaches the water concentration value in the Nafion® wall, no more water can be absorbed and drying stagnates. The remaining concentration of water in the Nafion® at the corresponding operating temperature determines the minimum water dew point that can be reached in the sample gas. At room temperature (20°C), the residual water remaining in the Nafion® corresponds to a water dew point in the gas of -45° C. This means that no lower dew point than -45°C can be reached at room temperature.
At higher temperatures, there is an approximate parallel shift in the minimum dew point, i.e. a dryer temperature of 60° C corresponds to a minimum dew point of -5° C. As condensation due to falling below the dew point must not occur under any circumstances, Perma Pure dryers must be heated when operating with gases of higher humidity. Heated dryers should have a temperature gradient over their length so that optimum drying is achieved. The optimum configuration would be one in which the temperature is just above the dew point of the sample gas at every point of the dryer. The differential pressure across the Nafion membrane influences drying via the water vapor partial pressures. At 13 bar, the burst pressure of the Nafion® tube is well above the maximum operating pressure of approx. 2 bar (differential pressure), depending on temperature and dryer type. The absolute pressure is of secondary importance. Nafion® is extremely corrosion-resistant. At the application temperatures and in the gas phase, there are hardly any known substances that attack Nafion®. The application is limited by the materials of the dryer housing (stainless steel, PTFE, PVDF or polypropylene) and the seals (fluororubber FPM).
Selectivity of the drying process
The only known components that are also transported through the Nafion® membranes are those with a hydroxyl group. As most inorganic hydroxides do not occur in the gas phase (except as aerosols), this group of components is essentially limited to:
In addition, organic components that hydrate or are converted into alcohols or enols (aldehydes, ketones) by the acidic catalysis of Nafion® (Nafion® is a strong acid) can also be transported by Nafion®. Although Nafion® does not only transport water, the selectivity of drying with Nafion® is much better compared to other types of drying.
Components | suitable | not suitable |
---|---|---|
Atmospheric gases such as:N2, H2, O2, noble gases | X | |
Oxides: CO, CO2, SO2, SO3, NOx | X | |
Halogens and halogen compounds: Cl2, F2, HCl, HF, HBr, halogenated hydrocarbons | X | |
Sulphur components: H2S, COS, mercaptan | X | |
Hydrocarbons (all simple hydrocarbons without functional groups) | X | |
Toxic gases such as: HCN, COCl2, NOCl | X | |
Toxic gases such as: HCN, COCl2, NOCl | X | |
Inorganic acids | X | |
Organic components such as: DMSO, alcohols; organic acids, aldehydes, ketones | X | |
Ammonia and ammonium compounds | X |
Typical installations
The simplest and most effective set-up is to operate the dryer with external drying gas in counterflow. It does not matter which gas is used. The dry gas flow should be approx. twice as high as the sample gas flow. Only when drying gases containing HCl must the dry gas flow be increased to 8 – 10 times the sample gas flow. If no dry gas is available, a partial flow of the dried sample gas can be diverted and used as dry gas. In order to build up a water partial pressure difference, the purge gas obtained in this way must flow through the purge gas chamber at negative pressure using a pump. The differential pressure across the Nafion® wall should be at least 500 mbar.
Maintenance of Perma Pure Nafion® dryers
Perma Pure dryers are maintenance-free as long as the surface is not contaminated by particles or condensate. It is therefore necessary to operate Perma Pure dryers only with filtered gases and to use a clean, oil-free purge gas. In the event of contamination, Perma Pure dryers can be cleaned. For this purpose, the Nafion® tube or the tube bundle is rinsed with solvents such as halogenated hydrocarbons, isopropanol, then with diluted hydrochloric acid and finally with purified water.
Further applications
As water always moves in the direction of the partial pressure gradient, Perma Pure dryers are also suitable for the selective humidification of gases. One of the most common applications is the humidification of dry sample gases or test gases for measuring methods that require a certain residual humidity.